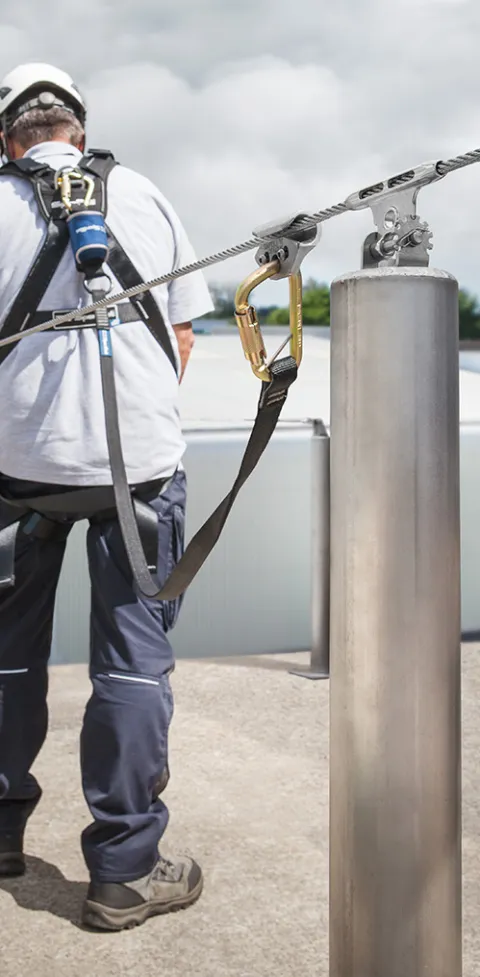
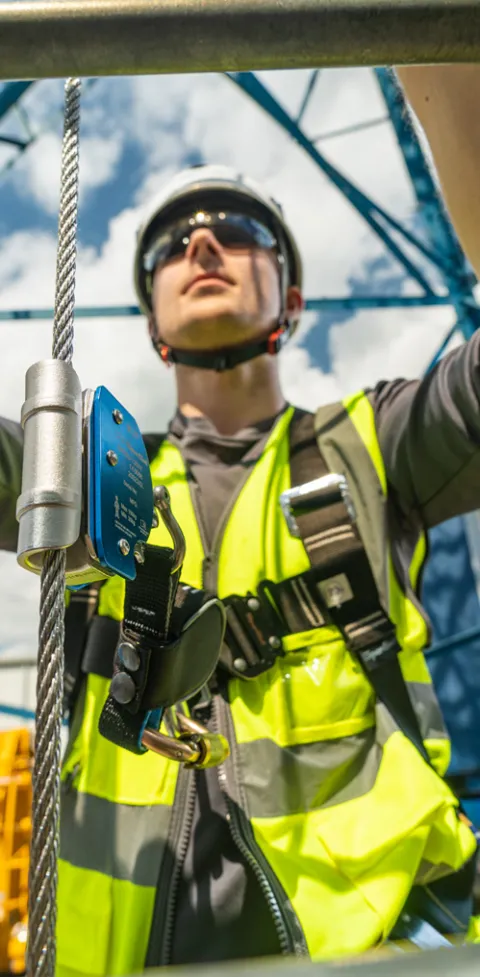
SpanSet Installed Height Safety Systems - Why a 'tick box' inspection from the ground isn't sufficient.
Having your SpanSet Installed Height Safety System inspected by us, offers -
Exceptional Standards, Peace of Mind and Value for Money.
All installed height safety systems need to be inspected, tested and recertified regularly to ensure they are safe to use. As the duty holder is responsible for staff and site operatives’ safety whilst on the premises it is critical to keep these systems maintained in good condition.
Why are Inspections necessary?
- Health & Safety Legislation - BS7883 requires installed Personal Fall Protection Systems are inspected and re-certified by a competent company/person annually. Systems installed in more extreme environments will be risk assessed and may require more frequent inspections
- Duty of Care – All responsible businesses want to ensure equipment is fit for purpose and safe for their workforce to use. No one wants accidents. A safety inspection of installed systems is an essential part of due diligence for any building where workers will be using these safety lines.
- Prevent problems in the future – regular inspections ensure deterioration or damage is reported promptly and avoids further problems arising from neglect. Weathering and wear and tear over time can damage the integrity of the fixings. SpanSet Installed Safety Systems are built to last, even in exposed or corrosive environments, however an inspection is required to ensure that systems still meet the standard of safety required for the activities that will be undertaken.
- Protect your guarantee – SpanSet cannot guarantee a product will meet its predicted lifespan if it hasn’t been inspected and maintained correctly by a suitably qualified person.
- Avoid costly delays - The need to gain access using an installed Personal Fall Protection Systems can occur at any time. It’s not advisable to assume the system will pass an inspection at the last minute or that it will be possible to find an approved company to carry out an inspection at short notice.
What should an Installed System Inspection include as a minimum?
- All Personal Fall Protection Systems are subject to pre-use inspection by workers. (Any worker that has received training by SpanSet to use the system safely will be capable of conducting pre-use checks).
- Risk Assessments and Method Statement for the works to be carried out.
- For systems installed at high level, suitable safe access equipment should be used/supplied.
- If Work at Height is required, suitable WAH equipment, training and rescue provision.
- Use of the correct tools to ensure fixings are tight and system is correctly tensioned.
- Pull testing of anchors where applicable.
- An “up close”, “hands-on” visual and physical inspection of all components including the wire rope, which requires access to both ends of and traversing the full length of the system.
- Certification and support with record keeping (access to duplicate certs).
Therefore a ‘tick box’ inspection from the ground isn’t sufficient.
So, who is considered competent to carry out a thorough examination of a SpanSet Installed Safety System?
- An Insurance Assessor would be considered competent to carry out a thorough examination inspection provided they can demonstrate they are trained and approved by SpanSet in Installation, Servicing and Repair of our systems in accordance with BS7883:2005 and EN795:2012. Approved Assessors will have access to our current technical documents, specifications and spare parts to maintain our systems and will be able to guarantee the safety of equipment.
- Installers of Fixed Systems would be considered competent to carry out a thorough examination inspection on a SpanSet Installed System provided they can demonstrate they are trained and approved by SpanSet in Installation, Servicing and Repair of our systems in accordance with BS7883:2005 and EN795:2012. Approved Inspectors will have access to our current technical documents, specifications and spare parts to maintain our systems. Should a fault be found and the system deemed non-compliant, they would be able to fix the problem and to guarantee the safety of equipment.
- A SpanSet Inspection - our dedicated Inspection and Maintenance Service supports our installations and is designed to take away the worry and maximise the product lifespan by offering a comprehensive inspection package.
Please contact the SpanSet Services Administration Team to verify whether a potential service provider has received training and approval to maintain our Installed Safety Systems.
A SpanSet Inspection - Exceptional Standards, Peace of Mind and Value for Money!
Trust our SpanSet Inspection Team to ensure your Installed Safety System is inspected, repaired, maintained and conforms to the highest of standards.
Our inspections include:
- Risk Assessments and Method Statements for the works to be carried out.
- Suitable safe access equipment for systems installed at high level is used/supplied. All Inspection Technicians are trained in IPAF and PASMA.
- Suitable Work at Height equipment, training and rescue provision is used where required.
- Use of the correct tools to ensure fixings are tight and system is correctly tensioned.
- Pull testing of anchors where applicable.
- An “up close”, “hands-on” visual and physical inspection of all components including the wire rope, which requires access to both ends of and traversing the full length of the system.
- Access to stock spare parts on the van so repairs can be completed in the same visit whenever possible.
- Ability to service fall arrest blocks in the back of the van
- Increased efficiency for multisite inspections grouping travel and access equipment hire.
- Certification and support with record keeping through our specialist asset management system (access to duplicate certs).
- Reminders ahead of when your systems are due inspection.
- Access to all associated products and services including training, equipment, consultation and installation.
- Options to use inspection services on demand or with a managed contract
Employers, building Owners, Occupiers, Management Companies, or the building’s Facilities Management Providers etc can be held responsible should an accident occur, particularly if equipment is found to be faulty and/or uncertified. The human and economic consequences of this are of course significant. A SpanSet Inspection by our professional Team offers real peace of mind and value for money.
Have a question? Need to book an Inspection? Complete our enquiry form here or call now on 01606 734279.e
Legal References:
All of the following publications require the employer to ensure the safe working condition of anchorage systems, including periodic examination by a competent person at least every 12 months:
The Work at Height Regulations 2005.
EN795: 2012 (Personal Fall Protection Equipment – Anchor Devices).
BS7883:2005 (Code of practice for the design, election, installation, use and maintenance of anchor devices conforming to BS EN 795).
BS8437:2005 (Code of practice for the selection, use and maintenance of personal fall protection systems and equipment for use in the workplace).