Many construction accidents involve lifting equipment. Statistics show that an average of 95 people suffer severe injuries in forklift accidents daily, equating to 34,900 serious injuries annually.
Other cases, as reported in the Bulletin Parampara, a communication medium from the Human Resources Development Agency (BPSDM) of the Ministry of Public Works and Public Housing (PUPR), include:
- Concrete detachment from a crane and the collapse of a box girder in the Jakarta LRT project,
- Accidents in elevated construction projects, and
- Two loading and unloading workers at PT. DABN Probolinggo port who died after being struck by a crane used to move cargo onto a ship.
Tragic, isn't it? 90% of such incidents result from human negligence and a lack of awareness regarding workplace safety standards. This is why periodic lifting equipment inspections are mandatory for companies.
The Benefits of Regular Lifting Equipment Inspections
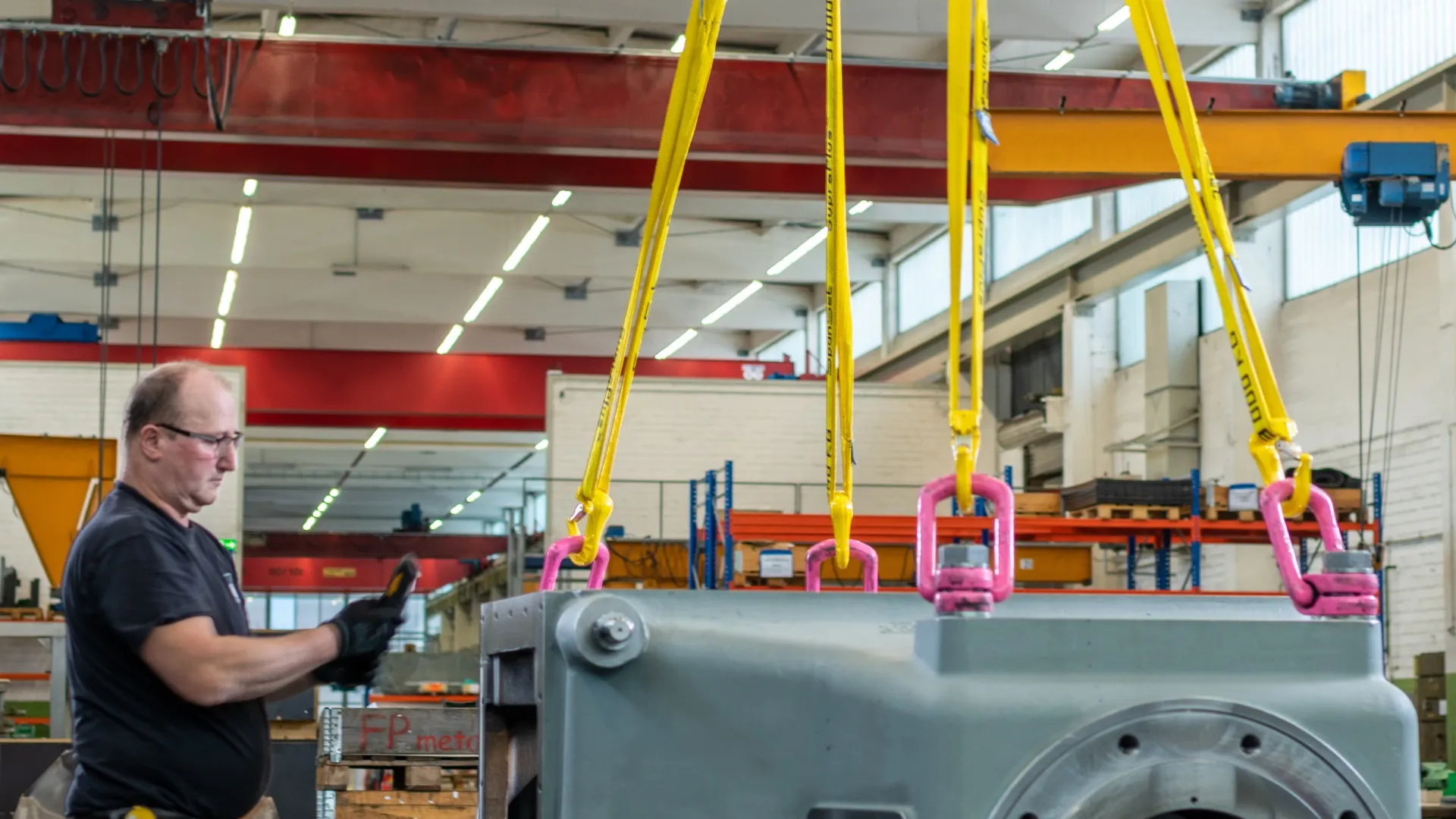
The Benefits of Regular Lifting Equipment Inspections
Lifting equipment inspection is not just a formality—it is a long-term investment for companies. Conducting regular inspections allows businesses to:
1. Ensure Worker Safety
Well-maintained equipment reduces workplace accident risks. Data indicates that many lifting equipment accidents occur due to a lack of routine maintenance.
2. Comply with Legal Standards
Regular inspections demonstrate that a company prioritizes safety and adheres to industry regulations. This also enhances your company's professional image in the eyes of clients.
3. Reduce Operational Costs
Inspections help detect potential damage early, preventing costly equipment failures. Repairing equipment before it breaks down completely is far more economical than purchasing new equipment. Additionally, it minimizes unnecessary downtime.
4. Improve Work Efficiency
Routine inspections ensure your lifting equipment is always in optimal condition. Properly functioning tools enhance team productivity and prevent workflow disruptions.
Read also: What is Riksa Uji? Why is it Important for Work Safety?
Lifting Equipment Inspection Procedures

Lifting Equipment Inspection Procedures
Lifting equipment inspection and testing are conducted in several stages:
1. Inspection Process
- Visual Inspection: Direct observation to detect visible damages such as corrosion, cracks, deformation, or wear on the equipment’s surface.
- Dimensional Inspection: Measuring various equipment components to ensure they comply with specified standards, including material thickness, diameter, and allowable tolerances.
2. Testing Process:
- Load Test: A load test is conducted to verify the equipment's ability to withstand its designated weight capacity.
- NDT (Non-Destructive Testing):
- Magnetic Particle Test: Uses magnetization to detect surface and subsurface defects in ferromagnetic materials.
- Penetrant Test: Uses a specialized penetrant fluid to identify minor cracks and defects on the material's surface.
These NDT methods are essential for ensuring the structural integrity of lifting equipment without damaging the tested materials.
Once all steps are completed, the equipment will be tagged and color-coded according to the inspection period.
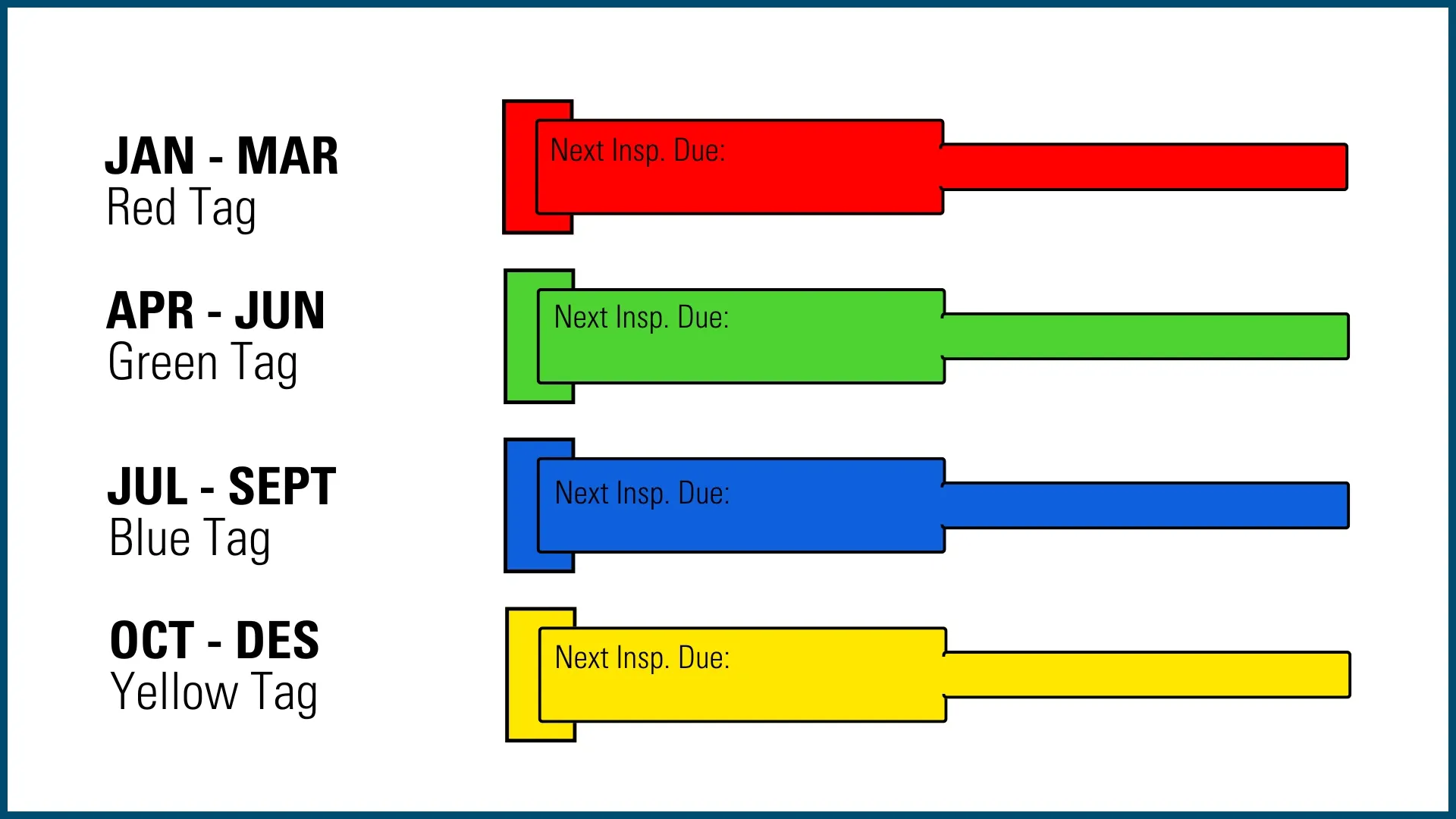
Read also: How Often Should Riksa Uji Be Conducted? Here's the Process!
Conduct Regular Inspections to Prevent Risks
Lifting equipment inspections are a crucial step in maintaining workplace safety. By implementing them, SpanSet partners can protect their company’s most valuable asset—its workforce!
Remember, routine inspections are not just about regulatory compliance; they are an investment in business sustainability and worker well-being.